Revitalising Heritage: Cannington Bottle Shop
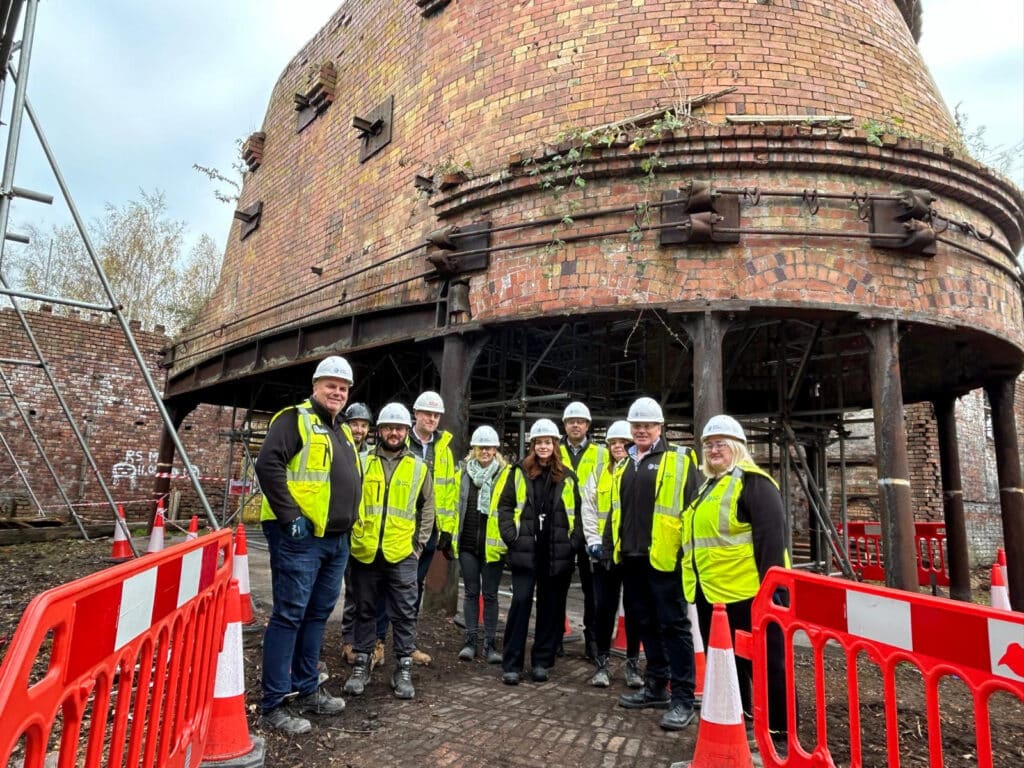
Our CDM team recently stepped back in time during a visit to the Cannington Shaw No.7 Bottle Shop in St Helens, one of Britain’s historic landmarks in glass-making.
Camellia House Wins Georgian Group Award
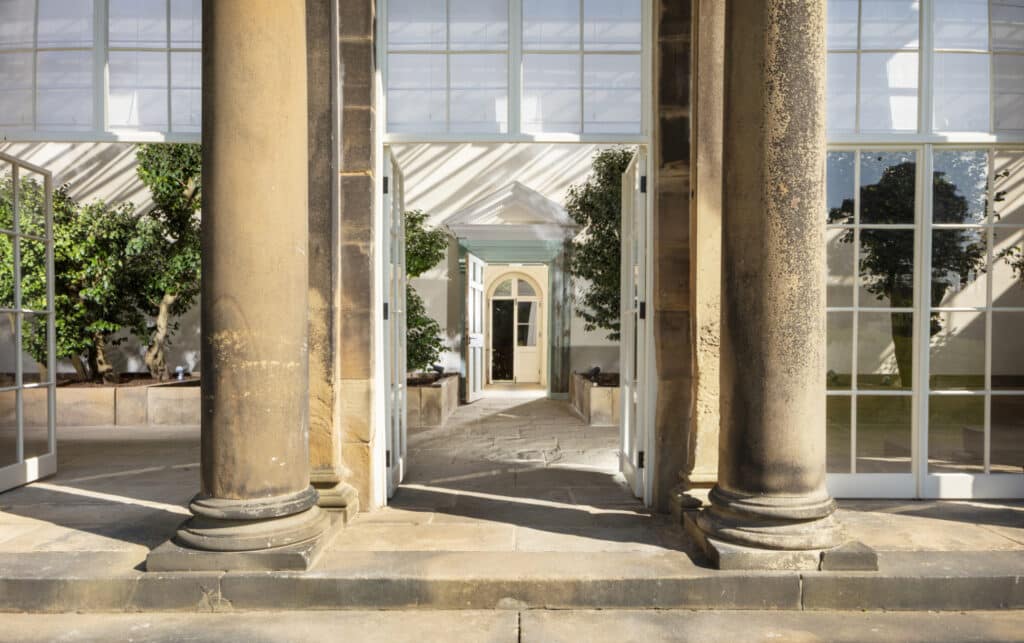
Camellia House Wins Georgian Group Award Safer Sphere is delighted to share that our client, Donald Insall Associates, received the prestigious ‘Re-use of a Georgian Building’ award for The Camellia House project at The Georgian Group Awards ceremony last night. We are proud to have provided Client CDM Assurance to the Wentworth Woodhouse Trust and […]
Camellia House Wins RICS Regional Award
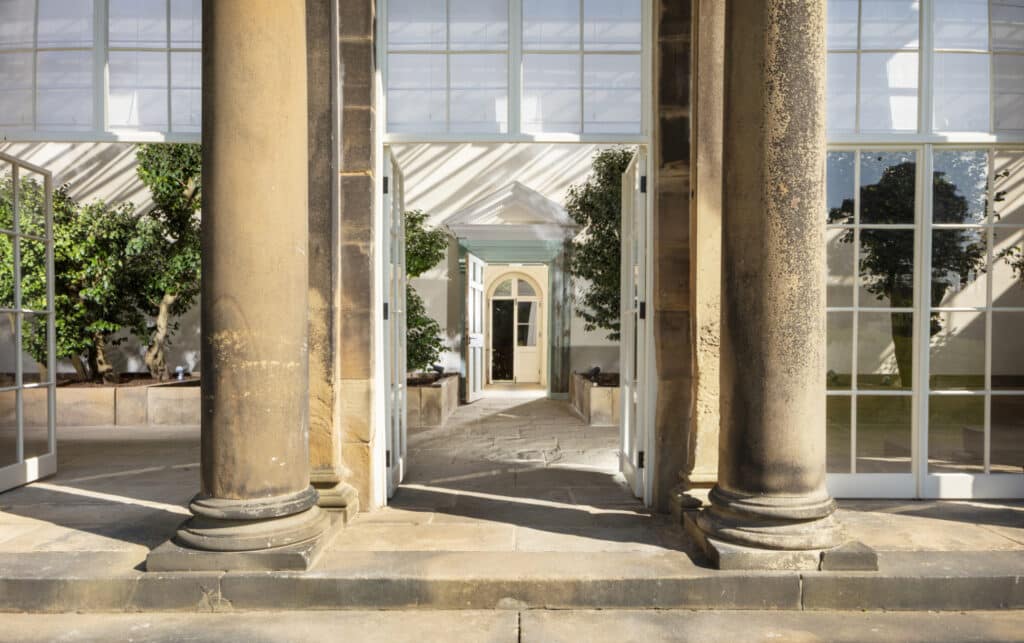
Safer Sphere is proud to announce that The Camellia House, a Grade II*-listed conservatory nestled within the Gardens of Wentworth Woodhouse, has received a RICS regional award in the Refurbishment/Revitalisation category
World Day for Health & Safety at Work
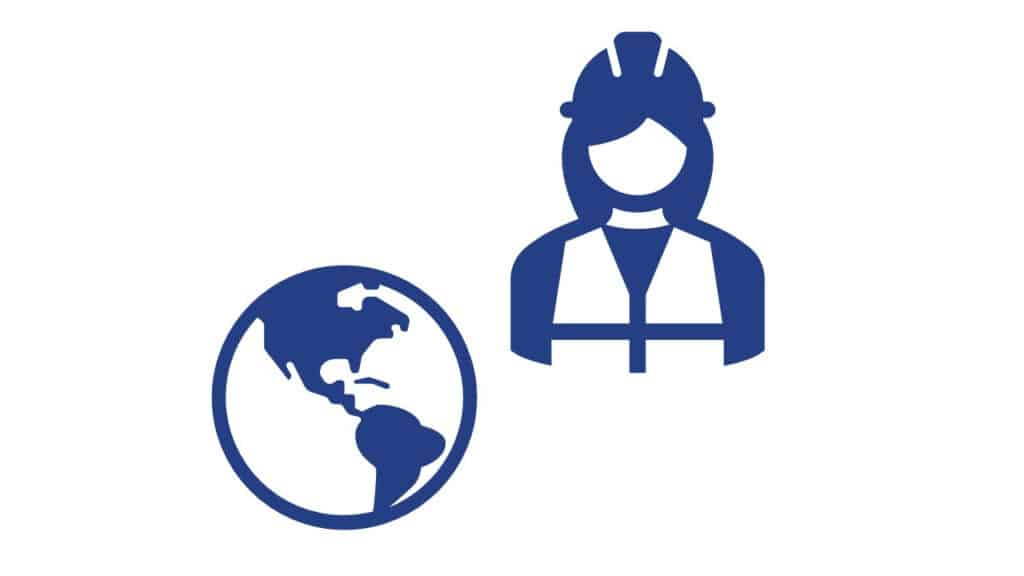
To mark World Day for Health and Safety at Work we have shared our Quarterly Health and Safety newsletter
APS Retained Accreditation Success
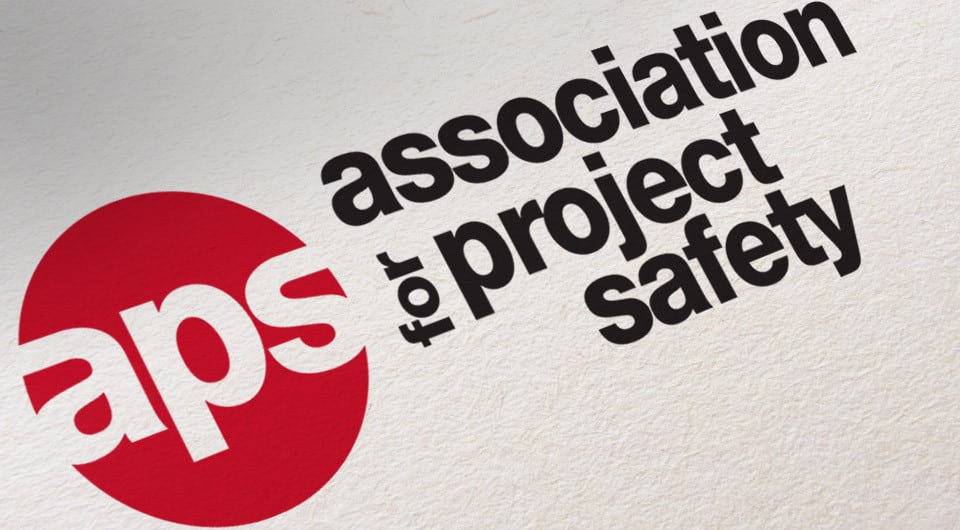
Safer Sphere is thrilled to announce the successful retention of our Principal Designer, Principal Designer Advisor, and CDM Advisor accreditations from the prestigious Association for Project Safety.
Safer Sphere Staff Communications Day
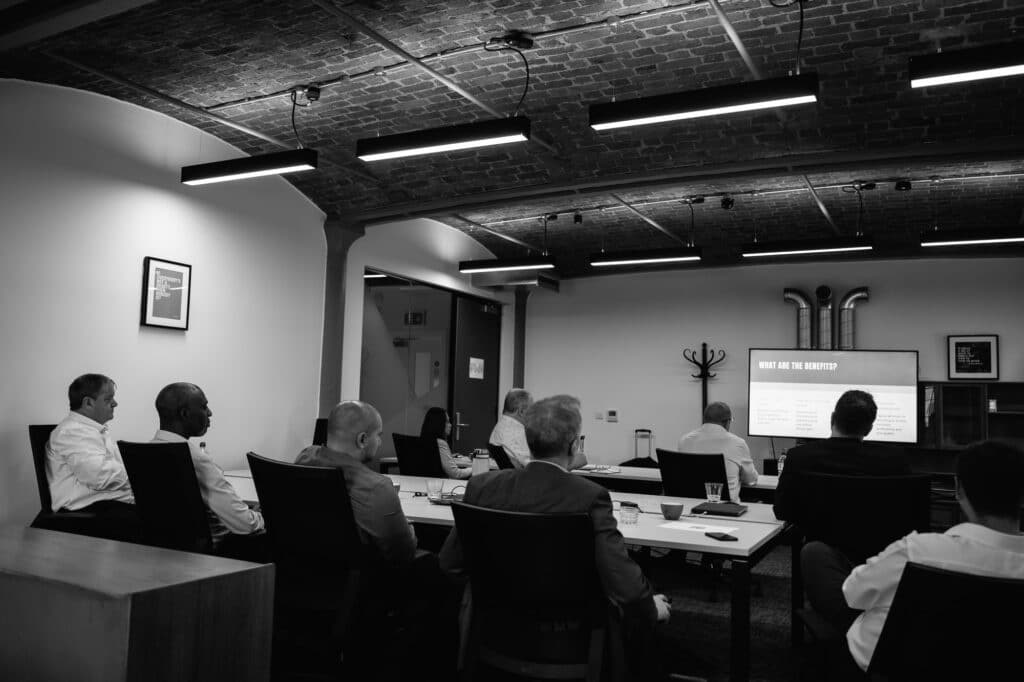
Safer Sphere’s Staff Communications Day Embraces Mental Health and Wellbeing
Safer Sphere Pedals 25 miles for PDA
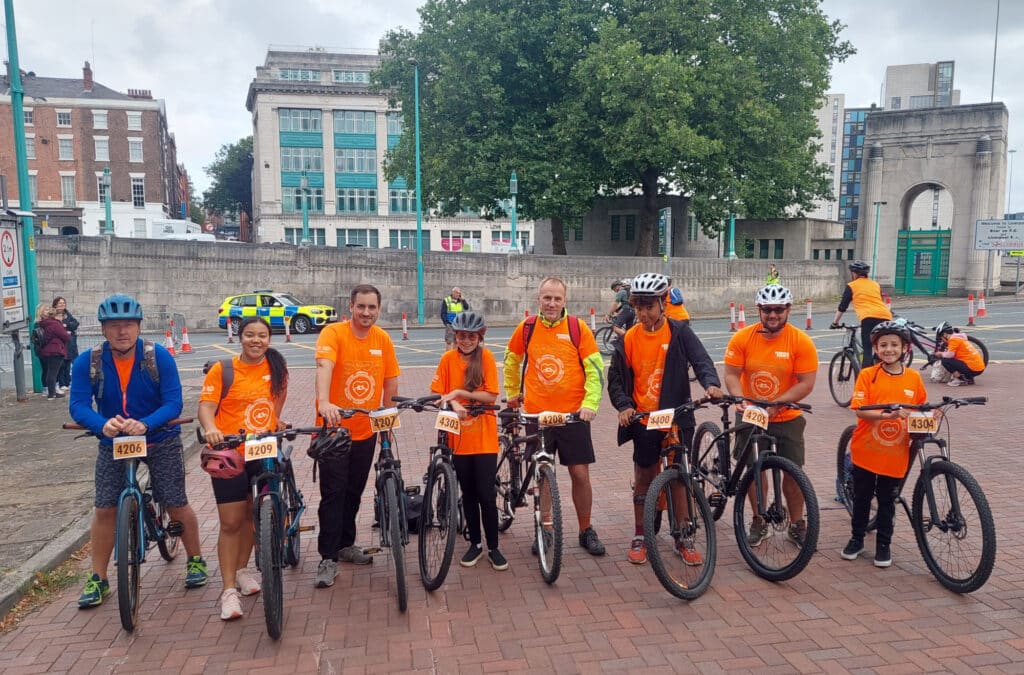
Join Us in Pedalling for PDA Awareness!
Plans Approved for One Medlock Street scheme in Manchester
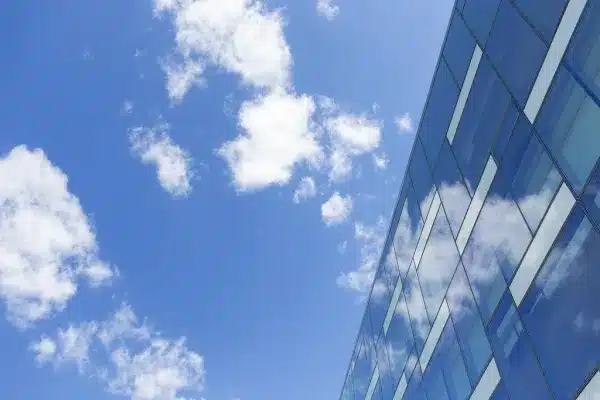
Safer Sphere is thrilled to be supporting Jon Matthews Architects’ on the exciting new project in Manchester
Safer Sphere Announces Changes to Board Structure
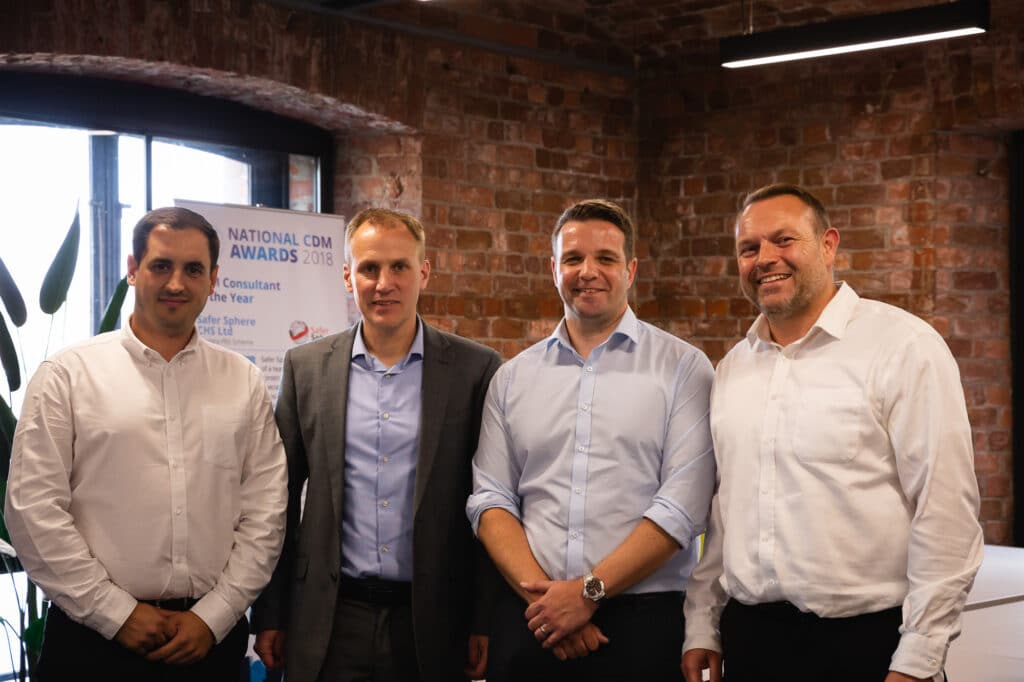
We have some exciting news to share!
Safer Sphere Welcomes Graham King as Associate Director of Building Safety
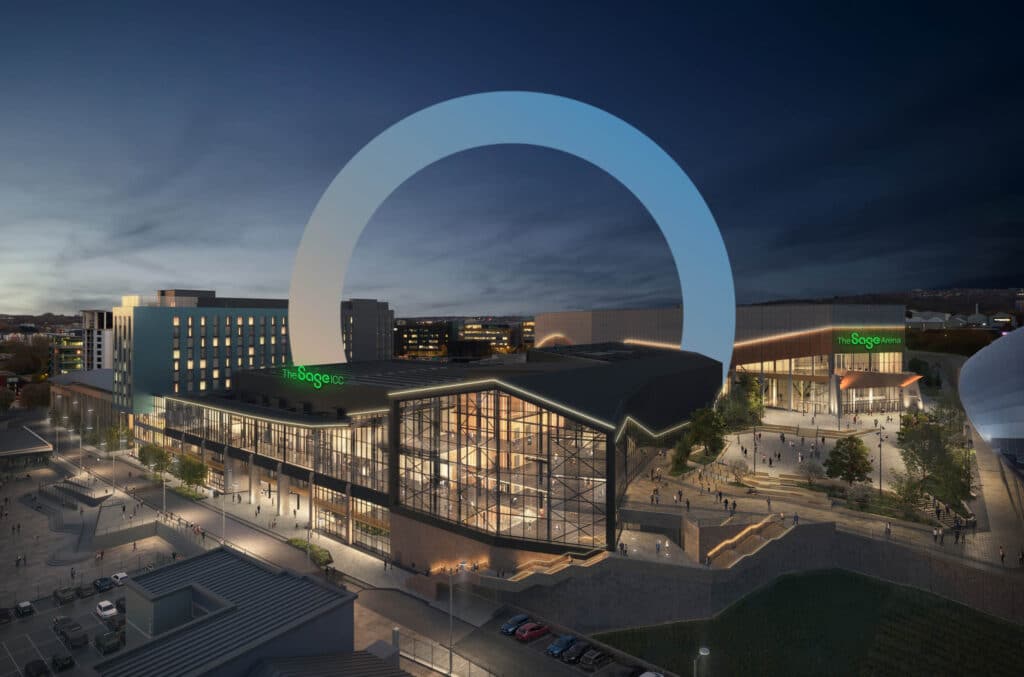
Safer Sphere expands team with new Associate Director of Building Safety